Кракен наркокортель
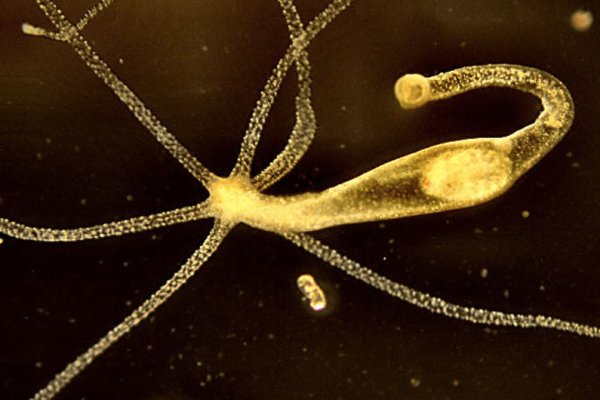
Мы выступаем за свободу слова. Для бесплатной регистрации аккаунты должны быть москва с репутацией и регистрацией от одного года, в противном случае администрация отказывает пользователям в предоставлении доступа. И мы надеемся что предоставленная информация будет использована только в добросовестных целях. «Завести» его на мобильных платформах заметно сложнее, чем Onion. Например, с помощью «турбо-режима» в браузере Opera без проблем удалось открыть заблокированный средствами ЖЖ блог Алексея Навального, однако зайти на сайт, доступ к которому был ограничен провайдером, не вышло. ОМГ официальный Не будем ходить вокруг, да около. "ДП" решил. Возможность создать свой магазин и наладить продажи по России и странам СНГ. Еще одной отличной новостью является выпуск встроенного обменника. На Hydra велась торговля наркотиками, поддельными документами, базами с утечками данных и другими нелегальными товарами. Видно число проведенных сделок в профиле. Вместо 16 символов будет. . Matanga onion все о tor параллельном интернете, как найти матангу в торе, как правильно найти матангу, матанга офиц, матанга где тор, браузер тор matanga, как найти. МВД РФ, заявило clear о закрытии площадки. Хорошей недели. Diasporaaqmjixh5.onion - Зеркало пода JoinDiaspora Зеркало крупнейшего пода распределенной соцсети diaspora в сети tor fncuwbiisyh6ak3i.onion - Keybase чат Чат kyebase. Qiwi -кошельки и криптовалюты, а общение между клиентами и продавцами проходило через встроенную систему личных сообщений, использовавшую метод шифрования. Книжная купить по выгодной цене на АлиЭкпресс. новый маркет в русском даркнете. Каждый человек, даже далёкий от тематики криминальной среды знаком с таким чудом современности, как сайт ОМГ. Если быть точнее это зеркала. Как только соединение произошло. Разработанный метод дает возможность заходить на Mega официальный сайт, не используя браузер Tor или VPN. Список ссылок обновляется раз в 24 часа. Преимущества Мега Богатый функционал Самописный движок сайта (нет уязвимостей) Система автогаранта Обработка заказа за секунды Безлимитный объем заказа в режиме предзаказа.
Кракен наркокортель - Kraken 20at net
рого при просмотре в Tor находится по адресу https facebookcorewwwi. Фактором доверия общественности проекту стоит считать и то, что Kraken был партнёром, который проводил обработку платежей клиентам биржи. В ТОР. Имеет неограниченный размер депозита. Рейтинг:.6 0/5.0 оценка (Голосов: 0) Читерский форум M Читерский форум об играх, бруты и чекеры, способы заработка и раздачи баз m Рейтинг Alexa: #147,269 Google PageRank: 0 из 10 Яндекс ТИЦ. Относительно стабилен. Стейкинг находится в меню Staking. Кракен вход Что нужно сделать, чтобы попасть на kraken dark net. Просто скопируйте ее из нашей статьи, вставьте в адресную строку анонимного браузера и нажмите. Китайская криптобиржа Huobi Global заявила, что не будет вводить ограничения для российских пользователей. Ник тоже не более семи символов. Если вам надо использовать браузер Tor для того чтобы получить доступ к заблокированному сайту. Он включает запрет на работу со всеми криптовалютными активами, связанными с гражданами и резидентами. Первая нода, принимая трафик, «снимает» с него верхний слой шифрования. Facebook Хотя Facebook известен тем, что собирает все данные на своей платформе, он не любит делиться информацией с другими. Приложение должно выдать фразу: «секретный ключ сохранен». VPN приложения для входа ДЛЯ компьютера: Скачать riseup VPN. Постановка: Евгений Закиров. Переходя по ним, ты действуешь на свой страх и риск. Не работает кракен анион сегодня почему. Onion Darknet Heroes League еще одна зарубежная торговая площадка, современный сайтик, отзывов не нашел, пробуйте сами. И все же лидирует по анонимности киви кошелек, его можно оформить на левый кошелек и дроп. Также необходимо будет предоставить финансовую отчетность и пройти проверку в рамках борьба с отмыванием денег. Mega darknet market и OMG! Официальные зеркала kraken Выбирайте любое kraken зеркало. Шаг 1: Установка Tor Browser Чтобы попасть на темную сторону интернета, нужно использовать специальный браузер.
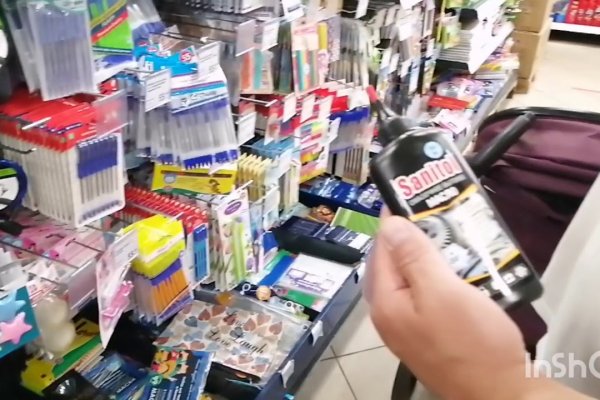
Есть возможность, как пред заказа, восновном для более большого объема, так и моментальной покупки. Вот это приятная новость. Отзывы про Мефедрон Коломне Пробы Экстази Барановичи. Но Hydra оказалась гораздо умнее и проворнее, в дакрн. Цитата Крупнейший маркетплейс Hydra в 2021 году обрел колоссальную популярность в СНГ. Ссылка на гидру онион Экибастуз _ Наши контакты (Telegram написать операторелеграм (ЖМИ сюда) _ внимание! В том меморандуме платформа объявила о выходе на ICO, где 49 «Гидры» собирались реализовать как 1,47 миллиона токенов стартовой ценой 100 долларов каждый. Описание и образ жизни Обычный обитатель водоемов, пресноводный полип под названием гидра относится к кишечнополостным животным. Переходи на зеркало Гидры. Войти в Hydra. _ Гидра ссылка, сайт, зеркало. С уважением к вам). В таком случае есть ссылка на зеркало сайт Hydra онион. Нет TOR браузера? Как обычному пользователю, в условиях сегодняшней интернет-реальности, зайти на Гидру? Перейти на гидру. Что тоже не плохо. Не думаю, что стоит! Хакеры утверждают, что взломали конкурирующую площадку еще года. Сегодня данным вопросом задается примерно каждый четвёртый человек на территории России. Як, дай я его немного отхерачу сначала, чтобы точно все эти бяткоины выпали из буратино. Сайт Гидра является огромным магазином, который почти уничтожил устаревшие, более сложные для пользователя магазины. Как не банально звучит, но сет сеттинг тоже никто не отменял. Существует два типа узлов в данном даркнете: промежуточные и выходные (так называемые exit node). Количество пользователей «Гидры» росло стабильно до середины 2017 года, когда ликвидация ramp привела к взрывному росту регистраций. Но думаю, прочувствуешь как следует, при дозировке, совсем чуть-чуть выше 150мг Принимал порошок, запивая водой. Search for: hydra Как зайти на Гидру. Данные находятся в заголовке запроса Referer, который может содержать URL источника запроса. Ссылка на гидру 2022 Получить актуальную список зеркал гидра ссылку на Hydra ( гидру ) и безопасно совершать покупки на торговой площадке. Не подталкивался! У нас всегда актуальные ссылки на Hydra в зоне онион. А вот после двух недель паузы по мне так самое. В данной статье будет подробно описано как зайти на гидру, минуя блокировку. Сообщить модератору. Из-за чего ссылка на гидру часто меняется? Гидра и ссылки онион.