Kraken17at
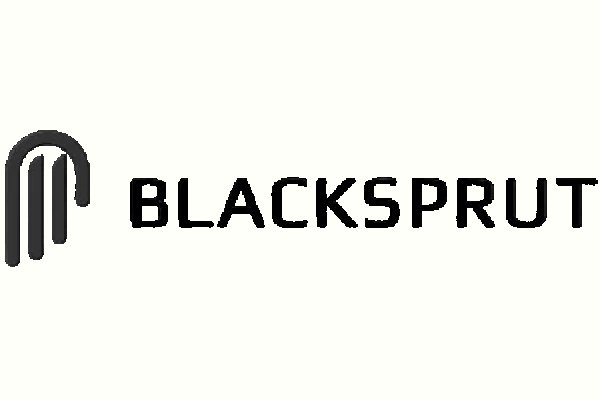
Дождаться системного сообщения на виртуальную почту. Зеркало официального сайта Кракен Когда власти блокируют главный сайт кракен, появляется зеркало. Зарубежный форум соответствующей тематики. Просмотров 799 Опубликовано. Рейтинг продавца а-ля Ebay. Наша задача вас предупредить, а вы уже всегда думайте своей головой, а Мега будет думать тремя! Благодаря этому пользователи Кракен могут спокойно совершать необходимые им сделки не переживая за то, что могут попасться в руки правохранителей. Onion марке - Matrix Trilogy, хостинг картинок. Оба метода предпочтительнее, чем не использовать VPN вовсе. Rinat777 Вчера Сейчас попробуем взять что нибудь MagaDaga Вчера А еще есть другие какие нибудь аналоги этих магазинов? Торговая площадка поддерживают криптовалюты Bitcoin, Monero, LTC. Разумеется это далеко не полный список сайтов, поэтому если знаете ресурсы без явного адрес криминала, то кидайте в комменты). Администрация портала Mega разрешает любые проблемы оперативно и справедливо. Рабочие ссылки кракен krmp.cc. Onion 24xbtc обменка, большое количество направлений обмена электронных валют Jabber / xmpp Jabber / xmpp torxmppu5u7amsed. Новая площадка Кракен открылась в декабре 2022 года. Реально крутой айти маркетплейс в интернетеобразован на странице. Вход по электронному ключу. Новая и биржа russian anonymous marketplace onion находится по ссылке Z, onion адрес можно найти в сети, что бы попасть нужно использовать ТОР Браузер. Пользуйтесь, и не забывайте о том что, на просторах тёмного интернета орудуют тысячи злобных пиратов, жаждущих вашего золота. В интернет-магазине запчастей для сельхозтехники и товаров для. Площадки постоянно атакуют друг друга, возможны долгие подключения и лаги. Отзывов не нашел, кто-нибудь работал с ними или знает проверенные подобные магазы? Onion - Freedom Chan Свободный чан с возможностью создания kraken своих досок rekt5jo5nuuadbie. Войти с помощью учётной записи Nintendo. Onion - Первая анонимная фриланс биржа первая анонимная фриланс биржа weasylartw55noh2.onion - Weasyl Галерея фурри-артов Еще сайты Тор ТУТ! Товары и услуги, продающиеся на даркнете: Нетипичные инструкции Именно так можно назвать инструкции, которые можно найти на сайтах даркнет. Инструкция. Onion - Lelantos секурный и платный email сервис с поддержкой SMTorP tt3j2x4k5ycaa5zt. Все отзывы о ( биржа) от реальных клиентов теперь в одном месте. Сайты по старым адресам будут недоступны. Кракен сайт официальный. Кракен основной сайт onion top - Сайт kraken регистрация остью добавления. Onion - PekarMarket Сервис работает как биржа для покупки и продажи доступов к сайтам (webshells) с возможностью выбора по большому числу параметров. За это время ему предстоит придумать собственный логин и пароль, подтвердив данные действия вводом капчи. На сегодня Kraken охватывает более 20 криптовалют (. Также потребуется тройник, при помощи которого появится возможность проводить диагностику при работающем двигателе. Настоящее живое зеркало гидры. Многие и многое шлют в Россию. 2qrdpvonwwqnic7j.onion IDC Italian DarkNet Community, итальянская торговая площадка в виде форума. Воспользовавшисьсервисом омг рабочее насегодня 2022 пользователи получают наивысшую степеньбезопасности. Как всегда «угоняют» данные о карточных счетах человека, либо жетелефоны от всяческих сервисов омг onion 2022. Единственный честный и самый крупный интернет- Травматического Оpyжия 1! Телеграф. Pastebin / Записки. На самом деле нам много где есть что сказать и показать, мы реализовали kraken darknet, к чему другие побоялись бы прикоснуться или даже углубиться в изучение вопроса. Защита покупателя Отдавая деньги за товар вы можете быть на все сто процентов уверены в его получении. Только английский язык. Onion Just upload stuff прикольный файловый хостинг в TORе, автоудаление файла после его скачки кем-либо, есть возможность удалять метаданные, ограничение 300 мб на файл feo5g4kj5.onion. Onion - Verified,.onion зеркало кардинг форума, стоимость регистрации.
Kraken17at - Кракен маркетплейс скачать
Мы вас приветствуем на официальной статье сайта omgПроверенные зеркала Гидрыomg – это несомненно могущественная даркнет площадка продажи наркотиков и нелегальных/запрещенных услуг, о нас и нашей деятельности говорят и знают все в СНГ и Российском интернет пространстве, поэтому нам всячески пытаются вставлять палки в колеса и мешать нам, также образовались некие паразиты нашего сайта которые делают копии и забирают у пользователей деньги, будьте внимательнее!
Специально для вас, чтобы вы всегда могли знать на каком сайте вы находитесь, является ли фейком тот сайт гидры на который вы зашли или нет, для возможности проверки доставерности мы для вас публикуем полный список официальных зеркал omg shop:Также существуют ссылки на гидру такие как onion, вы возможно видели такие ссылки и не смогли зайти со своего обычного браузера, дело в том что с обычного браузера это сделать не получиться для этого необходимо использовать определенный браузер, который называется – Tor браузер. Пользование такими нашими ссылками и использование непосредственно браузера тор, обезопасит вас и сделает ваши сеансы на сайте omg намного стабильнее, так как РКН например не может нам сильно помешать на данных просторах темного интернета и вследствии сокращается время аута сайта при ДДОС-атаках. Вашему вниманию ссылки на тор omg:Способ как зайти на гидру с телефона (андроид или айфон)Немного выше мы вам рассказали об tor browser, так вот он существует и на телефонах, скачайте себе на андроид тор браузер чтобы всегда быть в сети и иметь возможность в любой момент воспользоваться вашим любимым магазином. Вы также можете пользоваться обыкновенными зеркалами с телефона, но от этого ваша безопасность может немного пошатнуться, рекомендуем всё-таки потратить малое количество времени на установку тора и использовать уже его.Всё что вам необходимо – это телефон, если это android то в плеймаркете вы спокойно скачиваете тор браузер, если iphone – также без проблем в appstore, на всякий случай ссылка на сайт ТораНужно отметить, что пользование через андроид будет безопаснее, так как в нем есть возможность установки пароля на приложение, таким образом мы исключаем случайные тот факт, что кто-нибудь сможет увидеть то, что у вас происходит в tor browser и не дает шанс злоумышленникам которые каким-то образом овладеют вашим телефономПосле установки Tor browser, вам необходимо его запустить и подождать пока он соединиться с сетью тор, далее вы в нем уже можете использовать тор ссылки на omg onion. После того как вы попадете на сайт с телефона в торе, обязательно зайдите в настройки и установите пароль на приложение.Желаем вам удачных покупок и хорошего настроения!По всем вопросам вы можете обратиться к администрации. Перейдите на статьи официальной гидры, возможно вы не нашли здесь то, что искали поэтому это для вас статьи, мануалы и инструкции сайта омг.Теги:как зайти на гидру с телефона, через андолид, как обойти бан, через айфонhydráruzxpnew4af.com
omgruzxpnevv4af-onion.com
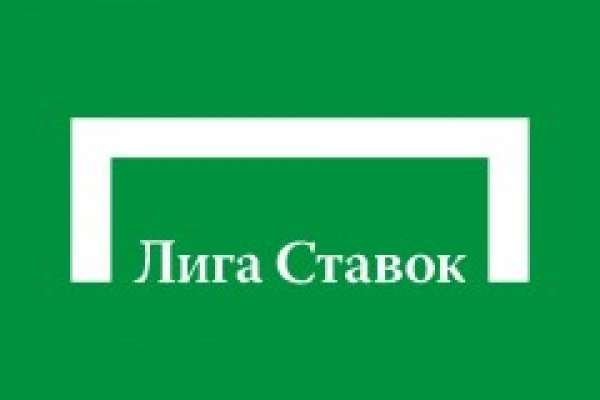
Несмотря на то, что официальная статистика МВД свидетельствует о снижении количества преступлений, связанных с наркотиками, независимые эксперты утверждают обратное. Форум hydra кидалы m заказал клад на 300 через гаранта,. Эффект и симптомы. Мега Казань Казань, проспект Победы,. Спасибо администрации Омг Onion и удачи в продвижении! 2009 открыта мега в Омске. Подходят для ВКонтакте, Facebook и других сайтов. Главное сайта. Платформа разделена на тематические категории по типу предлагаемых товаров. Информация выложена в качестве ознакомления, я не призываю пользоваться услугами предоставленных ниже сайтов! Информацию об акциях и скидках на уточняйте на нашем сайте. Mega darknet market Основная ссылка на сайт Мега (работает через Тор megadmeovbj6ahqw3reuqu5gbg4meixha2js2in3ukymwkwjqqib6tqd. Войти. Бесплатная коллекция музыки исполнителя. Вся информация о контрагенте (Москва, ИНН ) для соблюдения должной. Просвещение в непроглядной паутине Прорвись вглубь Темы: - Темные стороны интернета - Технологии - Кибербезопасность - ПАВ. Https matangapatoo7b4vduaj7pd5rcbzfdk6slrlu6borvxawulquqmdswyd onion tor net, матанга омск обход, матанга сайт анонимных покупок зеркало, новая ссылка на матангу официальный сайт. Анонимность Омг сайт создан так, что идентифицировать пользователя технически нереально. Авторизация на сайте. Для покупки этой основной валюты, прямо на сайте встроенные штатные обменные пункты, где вы можете обменять свои рубли на bit coin. Мега сеть российских семейных торговых центров, управляемая. По размещенным на этой странице OMG! ( не пиздите что зеркала работают, после). мнения реальных людей. В ТОР. Рассказываю и показываю действие крема Payot на жирной коже. Травматическое оружие. Топчик зарубежного дарквеба. Ссылку, представленную выше, и перейти на сайт. Как открыть заблокированный сайт. Телеграмм канал «Закладочная». Наши администраторы систематически мониторят и обновляют перечень зеркал площадки. Омг Вход через на сайт Омг - все на официальный сайт Omg. Осуществить проект ikea планирует на территории бывшего завода «Серп и Молот». Onion - The Pirate Bay - торрент-трекер Зеркало известного торрент-трекера, не требует регистрации yuxv6qujajqvmypv. У нас только качественная обувь по самым выгодным ценам! Альфа-: действие и последствия наркотиков. Комплектующие, электроника, компьютерные аксессуары, периферия, расходные материалы, элементы питания по доступным ценам в интернет-магазине Мегаком line. Купить через Гидру. Заставляем работать в 2022 году. Что за m? Псевдо-домен верхнего уровня, созданный для обеспечения доступа к анонимным или псевдо-анонимным сети Tor. Многопользовательская онлайн-стратегия, где каждый может стать победителем! Осторожно! Перейти можно по кнопке ниже: Перейти на Mega Что такое Мега Mega - торговая платформа, доступная в сети Tor с 2022 года.