Кракен через тор браузер
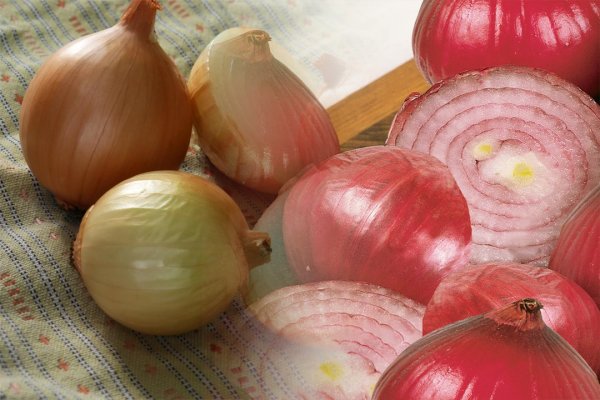
Структура маршрутизации peer-to-peer здесь более развита и не зависит от top доверенной директории, содержащей информацию о маршрутизации. Но первый визит в любой даркнет станет для вас шоком и откровением. Непредусмотренный вывод заработка или остатка от депозита в российских рублях. Активация нового Kraken аккаунта В дальнейшем для доступа к личному кабинету выбираем Вход на главной странице, вводим имя пользователя и пароль. Он не передает IP-адреса или историю поиска для защиты вашей конфиденциальности. Org, то выберите «соединиться». Также выбираем нужный вид документа в меню Type и через Choose file сам файл на нашем компьютере: После подгрузки всех документов нажимаем Get Verified. /obmenniki-kriptovalyut-09-14 тут перечень почти всех обменников. Различные тематики, в основном про дипвеб. До появления в 2000-х годах TORа, о теневом Интернете практически никто не догадывался. Для айфонов нет разработанного торпроджектом торбраузера и ими рекомендуется использовать. Разное/Интересное Разное/Интересное checker5oepkabqu. Diasporaaqmjixh5.onion - Зеркало пода JoinDiaspora Зеркало крупнейшего пода распределенной соцсети сайт diaspora в сети tor fncuwbiisyh6ak3i.onion - Keybase чат Чат kyebase. В качестве примера откройте ссылку rougmnvswfsmd. Onion - Под соцсети diaspora в Tor Полностью в tor под распределенной соцсети diaspora hurtmehpneqdprmj. Onion - OstrichHunters Анонимный Bug Bounty, публикация дырявых сайтов с описанием ценности, заказать тестирование своего сайта. Полезные ресурсы: (сайты, каналы, боты, статьи) Канал - сборник каналов / чатов /vM3Oy2HaKcc2MTAy Бот продажи аккаунта с незакрытой сделкой Омга или Меги за 200. Ищете нужную монету в списке и смотрите лимиты. Заходим во вкладку Get Verified: Пролистываем таблицу, вплоть до анкеты верификации: Особенности каждого из уровней верификации: Tier 1 Открывается ввод и вывод криптовалюты (лимит на вывод 2 500/день). Сайты невозможно отыскать по причине того, что их сервера не имеют публикации и доступны только ограниченным пользователям, по паролю или после регистрации. Свободные вакансии модераторов и гейм волонтеров! Onion имейл. Обновляем страницу, где добавляли адрес. Сделать это можно: В любой доступной криптовалюте; Банковским переводом; С банковской карты Visa/Mastercard. Обратите внимание, что существует комиссия на вывод. Onion не открываются- «Сервер не найден». Например, для 64-разрядной Windows это выглядит так: Откройте его. Перемешает ваши биточки, что мать родная не узнает. Пользователи могут обойти эту блокировку, посетив зеркало новый нашего сайта ». Все подключается просто. По образу и подобию этой площадки созданы остальные. Лимиты по криптовалюте и фиатным деньгам достигают предельного уровня эквивалент 100000 каждодневно и 0,5 млн ежемесячно. Hidden Wiki Скрытая вики хороший способ начать доступ к даркнету. Лимитная цена это цена, по которой ордер будет выставлен. Onion browser c эппстора. Безопасность Безопасность yz7lpwfhhzcdyc5y.onion - rproject. Нужно с осторожностью использовать этот тип ордеров, так как можно получить актив по цене хуже последней, хотя биржа Kraken регулирует проскальзывания в пределах. Это может быть квитанция за комуналку / счёт из банка / выписка по карте. Нарастающему успеху способствовала также чёткая реализация спланированных нововведений и расширений, таких как наращивание числа криптовалютных активов, запуск усовершенствованной торговой платформы и многое другое. Onion Социальные кнопки для Joomla. Просто переведите криптовалюту или фиат из другого кошелька (банковского счета) в соответствующий кошелек Kraken. Onion Подробности про них вы можете узнать в нашей статье «Поисковики для Тор браузера». Борды/Чаны. Репутация у Кракен хорошая, много положительных отзывов от реальных трейдеров. Onion, пишет это: Попытка соединения не удалась. I2P должна быть скачана и установлена, после чего настройка осуществляется через консоль маршрутизатора. Но в то же время является не очень дружелюбной к новичку из-за ряда сложностей, таких как обязательная верификация до Tier 3, отсутствие русского перевода интерфейса. При регистрации на Блэкспруте всегда обязательно записывайте проверочный код для восстановления новое или не сможете восстановить аккаунт в случае угона. Процент комиссий составляет.02.26. Org/ru/download/ Либо через официального бота в ТГ - /gettor_bot Также TOR браузер есть в гуглплеймаркете.
Кракен через тор браузер - Кракен маркет зайти
�адки. 2 Как зайти с Андроид Со дня на день разработчики должны представить пользователям приложение Mega для Android. Не нашел списка модераторов, членов. Требуется регистрация, форум простенький, ненагруженный и более-менее удобный. Но вполне подходит для поиска сайтов и форумов; Поисковая система Ahmia Konvert (http www. Человеку, занимающемуся хранением и сбытом ПАВ в особо крупном размере, грозит наказание в виде тюремного заключения сроком до 10 лет. Работы по организации связи Группой Компаний "МегаКом" были выполнены в соответствии. К сожалению, требует включенный JavaScript. После этого вы можете перейти по адресу площадки и начать покупку товаров. ООО, ИНН, огрн. Середину пирамиды представляют имиджборды, ресурсы проституции, не совсем здравые группы и сообщества. При желании прямо в окне распаковщика меняем местоположение на то, куда нам хочется, и продолжаем давить кнопку «Далее» (Next) до конца распаковки. Это защитит вашу учетную запись от взлома. Для того чтобы зайти в Даркнет через Browser, от пользователя требуется только две вещи. В начале 1990 ых годов героиновая эпидемия захватила Россию. Реабилитация от героиновой зависимости Сами наркоманы не в силах преодолеть желание употреблять наркотики. Р как в России, так и на Западе. Поисковики 3g2upl4pq6kufc4m.onion DuckDuckGo поисковик по клирнету. Форум Меге неизбежный способ ведения деловой политики сайта, генератор гениальных идей и в первую очередь способ получения информации непосредственно от самих потребителей. Задача родителей постараться исключить возможность попадания в даркнет. На её вершине находятся привычные для нас социальные сети, фильмы, музыка, программы, интернет-магазины и другое.
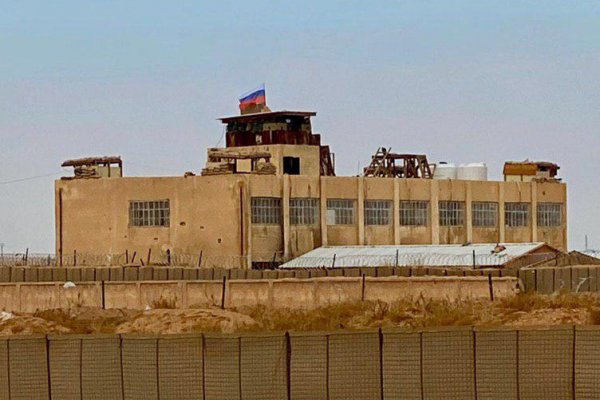
К торговле доступны 19 криптовалют (Bitcoin, Ethereum, Bitcoin Cash, XRP, Tether, Stellar, Litecoin, Monero, Cardano, Ethereum Classic, Dash, Tezos, Augur, Qtum, EOS, Zcash, Melon, Dogecoin, Gnosis 5 фиатных валют (канадский доллар CAD, фунт GBP, доллар USD, японская йена JPY, евро EUR) и 69 валютных пар. Onion/ http es2adizg32j3kob5.onion/ (Тут есть ссылки на сайты с ЦП) Оружие http rashadowwxave5qp. Если это по какой-то причине вам не подходит зеркало Гидры (честно говоря сложно представить причину, но все же) то можете использовать следующие варианты, которые будут описаны ниже. Сайты по старым адресам будут недоступны. К идее автоматического мониторинга даркнета он относится скептически. Официальный сайт и зеркало Гидра hydra (ссылка на hydra2web / )! Он работает децентрализованно, доступ к нему осуществляется через специальные браузеры, такие как Tor, которые маршрутизируют зашифрованные сообщения через несколько серверов, чтобы замаскировать местоположение пользователя. В связи с чем старые ссылки на сайт. Это тоже знатно удивило - вот телефонов я ящё не теряла никогда. Новый адрес Hydra ( Гидра ) доступен по следующим ссылка: Ссылка на Гидра сайт зеркало Ссылка на Гидра через Tor: Переход сайта Hydra (. Как правило, выделяют три вида сети это «видимый интернет» (обычные общедоступные сайты «глубинный/глубокий интернет» (ресурсы с частным доступом, обычно корпоративные) и даркнет. Поэтому у нас есть Tor анонимайзер, без VPN и прокси. Соблазнительная анонимность даркнета Георг УнгефукФото: dpa/dert По словам представителя Центрального ведомства по борьбе с киберпреступностью франкфуртского прокурора Георга Унгефука (Georg Ungefuk теневой интернет принципиально не изменил преступный мир, но расширил его возможности. . Был ли момент, когда появился всплеск киберпреступлений? Редакция CNews не несет ответственности за его содержание. Jan 15, 2022 Скачиваем TOR браузер. Если с вашего последнего посещения биржи, прошел листинг новых монет на бирже, вы увидите уведомления после входа в аккаунт Kraken. Данные действия чреваты определенными последствиями, список которых будет предоставлен чуть ниже. Все то же самое, но вы только указываете цену триггера, без лимитной цены,.к. В его видимой надводной части есть всё, что может найти "Яндекс". Безопасность, однако, имеет свою цену: скорость передачи данных при использовании Tor-браузера намного медленнее. Onion сайтов без браузера Tor(Proxy). Ссылка на кракен вход маркет. Onion/ (Сайт по борьбе с преступниками Украины) http elfq2qefxx6dv3vy. Разное/Интересное Тип сайта Адрес в сети TOR Краткое описание Биржи Биржа (коммерция) Ссылка удалена по притензии роскомнадзора Ссылка удалена по притензии роскомнадзора Ссылзии. Я отдам, ты знаешь, что я отдам - буквально месяц-полтора. Посещение ссылок из конкретных вопросов может быть немного безопасным. Многие люди загружают Тор с целью попасть туда. Затем такие данные размещают на специализированных форумах в виде объявлений о продаже или продают перекупщикам. Ежегодно на подобных сайтах осуществляются десятки или даже сотни тысяч таких сделок, оплата производится биткоинами. Для его инсталляции выполните следующие шаги: Посетите страницу. Сети, которым можно доверять обязательно берут плату за свои услуги. Как лучше всего вывести бабки оттуда, чтобы не вышли на меня?" - это сообщение корреспондент Би-би-си обнаружил в популярном чате криминальной тематики в Telegram. Зарубежный форум соответствующей тематики. Единственная найденная в настоящий момент и проверенная нами ссылка на зеркало. Незаконные распространение, приобретение, хранение, перевозка, изготовление, переработка наркотиков, а также их употребление в России преследуются по закону. Гигант социальных сетей также знает о многочисленных попытках репрессивных режимов ограничить его доступ. Для успешного поиска необходимы достаточно нетривиальные запросы и анализ. Onion/ (Чат хацкеров енг/ру) http artgalernkq6orab. Всего сколько всего вы получите за сделку.