Кракен сайт kr2web in официальный ссылка
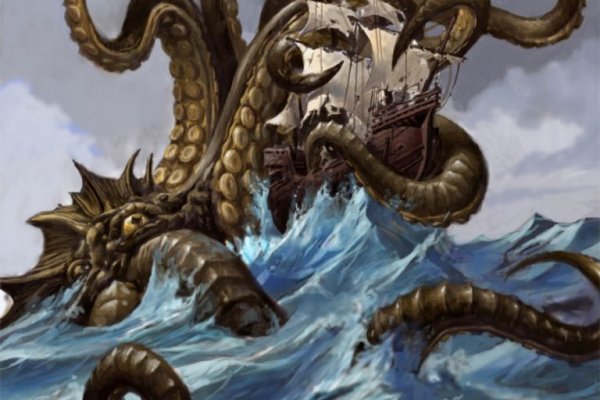
Подробней РР 01/06/200 РР 01/06/200 - рампа разрядная на 6 баллонов. . Фото слева: коллектор с шаровыми кранами Ду15. . На одной ветви происходит наполнение баллонов, на второй замена наполненных баллонов. Компактность (сокращение площади хранения в 10 раз). Преимущества ломозаготовителя: Низкие разовые вложения, относительно пресс-ножниц. От того, как он выполнен будет зависеть продуктивность работы персонала и всего газификатора. Нержавеющая сталь aisi 304 используется во всем мире ведущими производителями криогенного оборудования. По функциональному исполнению: как составная рампа- коллектор состоящий из унифицированных звеньев, собранных посредством резьб друг с другом. Скачай расчет тут. Криогенный регулятор подъема давления Ду15. Мы устанавливаем мощный и дорогой регулятор давления, который обеспечит плавный и быстрый набор давления. ГХК 0,5/1,6-30 всего за 8500 USD с НДС. Простой газификатора влечет за собой простой рабочих и дорогого оборудования (лазерный/плазменный станок.). Наше оборудование сертифицировано, имеется сертификат и декларация соответствия ТР ТС 032/2013. Фото справа: коллектор с вентилями Ду4. Баллонный вентиль просто не будет успевать пропускать тот объем газа, который вам необходим. Почему вам необходим газификатор, вы можете спросить у наших менеджеров. Подробней вперед). Каталог готовых решений на базе криогенных газификаторов вы можете скачать тут. Рампы ДЛЯ всех видов газов снабжаем больницы рампами ДЛЯ кислорода Популярные модели газовых рамп Рампы наполнительные Предназначены для наполнения баллонов сжатыми техническими газами Азот, кислород, аргон, гелий, углекислота и другие. Отсутствие возможности продать кислород «налево». А кракен оформив рампу в фирменном стиле компании, вы получите оригинальную рекламную площадку, которая точно привлечет внимание аудитории. Экономия затрат на кислород до 57, отностительно баллонов. Сегодня можно встретить на рынке изобилие синонимичных названий данного вида оборудования: рампа баллонная, газовая рампа, разрядная, расходня рампа, перепускная и проч. Коллектор на выдачу газа потребителю. ООО "Крионика" постоянно контактирует со своими клиентами, и занимается запуском и настройкой газификаторов, поэтому мы знаем, какие неприятности грозят потребителю при низкой температуре продукционного газа (выход из строя редукторов, перемерзание рукава, выход из строя сопла). Меньше ребер - меньше производительность, низкая температура газа на выходе - выход из строя редукторов и шлангов. Далее мы приведем небольшую классификацию данного оборудования. Почему вам стоит приобрести именно наш газификатор? ВЫ уже утомлены и мы не будем зацикливаться на тех усовершенствованиях,которые как не экономят ВАМ деньги, но делают работу с оборудованием приятной и легкой: все колтельный. Наполнительная рампа оборудована запорным отсечным вентилем, манометром и предохранительным клапаном.Изготавливаем рампы с двумя "ветвями это позволяет производить наполнение баллонов непрерывно. Подробней РР 01/15/200 РР 01/15/200 - рампа разрядная на 15 баллонов. . Скупой платит в первый раз. Такой регулятор обычно ставят на емкостью объемом в 16 раз больше, так что простоев не будет. Скупой платит трижды. Собственное производство, внедрение передовых технологий и использование высококачественных материалов позволяет нам решать комплексные инженерные задачи при проектировании и разработке и возводить уникальные архитектурные формы из бетона, асфальта, металла и дерева, отвечающие самым высоким международным стандартам. Мы сами вышли из индустрии экшн-спорта и до сих пор тесно общаемся с аудиторией, поэтому отлично понимаем ее потребности. ИЛИ обратиспециалисту: info Технические характеристики: геометрический объем: 500 литров эффективный объем: 475 литров рабочее давление: до 16кгс/см2 производительность: до 30 нм3/час. Разрядная рампа от 15 000 рублей Перепускная рампа от 25 000 рублей Наполнительная рампа от 17 000 рублей скачать технико-коммерческое предлож. О продукции Рампа газовая - это элемент трубопровода высокого давления, с помощью которого к линии потребления подключается необходимое количество газовых баллонов. Разрядная рампа от 15 000 рублей Перепускная рампа от 25 000 рублей Наполнительная рампа от 17 000 рублей Скачать технико-коммерческое предложение по рампам азот, аргон, углекислый ГАЗ (N₂, Ar, CO₂ газовая смесь. Составляем техническое задание Под каждый проект составляем индивидуальное Техническое задание и разрабатываем 3Д-модель рампы.
Кракен сайт kr2web in официальный ссылка - Кракен сайт купить наркотики
Средний уровень лимит на вывод криптовалюты увеличивается до 100 000 в день, эквивалент в криптовалюте. Так как все эти действия попадают под статьи уголовного кодекса Российской Федерации. Этот тип ордера защищает вас от сильного проскальзывания, но при сильных движениях на рынке ваша заявка может исполниться не до конца. Редакция: внимание! Он в числе прочего запрещает гражданам и резидентам России владеть криптовалютными кошельками, создавать учетные записи или хранить цифровые активы на территории еврозоны независимо от суммы депозита. I2P не может быть использована для доступа к сайтам.onion, поскольку это совершенно отдельная от Tor сеть. Это вовсе не проблема, а специфичная особенность, и с ней придется смириться. Это отличный вариант, если вы хотите анонимно просматривать веб-страницы. Обрати внимание: этот способ подходит только для статей, опубликованных более двух месяцев назад. Org b Хостинг изображений, сайтов и прочего Хостинг изображений, сайтов и прочего matrixtxri745dfw. Открой один материал Заинтересовала статья, но нет возможности стать членом клуба? Просмотр. К OTC сделкам в настоящий момент доступны следующие валюты: Фиатные валюты Доллар США (USD Евро (EUR Канадский доллар (CAD Японская иена (JPY Британский фунт (GBP). Поэтому если пользователь лично не раскроет свои данные, на взлом аккаунта у мошенника уйдет немало времени и сил. Однако многие новостные организации и издатели создали свои собственные URL-адреса SecureDrop, чтобы использовать возможности анонимных осведомителей. Onion - Harry71, робот-проверяльщик доступности.onion-сайтов. UPD: похоже сервис умер. Словарь терминов Склад человек, хранящий у себя большие объемы наркотиков, реализующий их через мастер-клады закладки с большим количеством вещества для кладмена. Публичный 1056568 Информационный канал теневого рынка кракен, вход - зеркалаонион. Для каждого актива она индивидуальна. Ежедневное обновление читов, багов. Указать количество монет. Mixermikevpntu2o.onion - MixerMoney bitcoin миксер.0, получите чистые монеты с бирж Китая, ЕС, США.
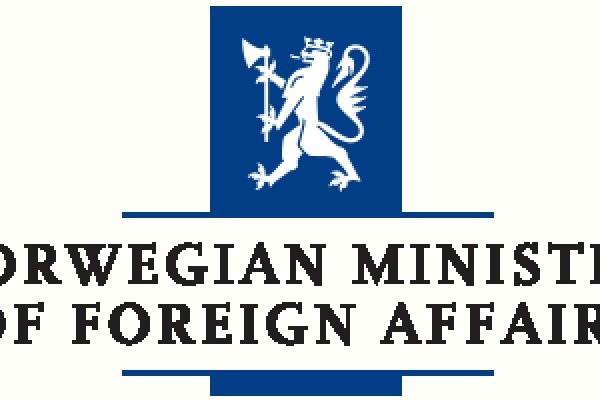
Что мы хотим видеть в идеальном браузере? В первую очередь, конечно, же, скорость. Скорость открытия и способ отображения страницы играет чуть ли не самую важную роль при выборе браузера. Немаловажен и набор функций: если приложение элементарно не умеет ставить закладку, оно совсем не нужно, не говоря уже о продвинутых фишках вроде встроенного VPN. И здесь мы плавно подошли к третьему критерию — приватности. Никому не хочется, чтобы за его перемещениями в сети постоянно следили, «догоняли» рекламой после посещения онлайн-магазина и показывали баннеры, которые зачастую мешают просмотру контента.Браузер со встроенным VPN и инструментами против отслеживанияНапример, вы посмотрели новый айфон или другое устройство (даже газонокосилку) в интернет-магазине, который настроил таргетинговую рекламу. Даже если вы найдете то, что искали, и купите это, магазин все равно может продолжить спамить рекламой — в Instagram, просто баннерами в браузере или даже в социальных сетях. Чтобы отгородить себя от этого, лучше пользоваться приватным браузером вроде Aloha Browser.Это не только бесплатный и очень быстрый веб-браузер (еще бы, со встроенным-то AD BLOCK), но и также VPN, сканер QR-кодов и многое другое. Но главное — Aloha Browser не ведет никаких записей о посещенных сайтах или ваших IP-адресах, не собирает никакой личной информации, и, соответственно, не сможет этим ни с кем поделиться, потому что делиться-то и нечем. Некоторые браузеры уже оказывались в центре скандала из-за передачи данных о своих пользователях на сторону, здесь же можно об этом не волноваться.Главный экран браузера позволяет быстро осуществить поиск, перейти на сайт из закладок или посмотреть новости (новостные категории можно отключить и кастомизировать так, как хочется). На эту страницу всегда можно попасть из нижнего навигационного меню.Справа размещена иконка для быстрого просмотра всех открытых веб-страниц (здесь же есть кнопка переключения частного доступа), по соседству — кнопка доступа к загрузкам. Приложение само распознает файлы или медиа (фото, видео, картинки) и группирует их по папкам.Вообще, по интерфейсу Aloha Browser чем-то напоминает родной Safari на iPhone. Это очень удобно, поскольку мы, например, не тратили много времени на то, чтобы привыкнуть к новому браузеру. Все кнопки размещены интуитивно и понятно, нет никаких лишних элементов, которые перегружают интерфейс. Но чего точно нет в Safari, так это отчета о приватности: данное приложение в режиме реального времени показывает, сколько вы сэкономили данных с его помощью (и времени), сколько раз рекламные трекеры пытались вас отследить и количество скрытий IP (приложение скрывает ваш реальный IP-адрес при включенном VPN). Мало того, если зайти в детальную статистику, можно обнаружить количество неправильных вводов пароля, вредоносные сайты и многое другое.Для активации VPN достаточно нажать на кнопку с щитом около строки поиска (адресной строки) — и ваше подключение сразу будет защищено. При этом можно быстро сменить страну подключения VPN, но лучше всего использовать быстрый премиум-сервер (это плюшка для владельцев премиум-подписки, но об этом чуть позже). Кстати, не так давно в Aloha Browser добавилась поддержка TOR — теперь можно посещать .onion сайты, просто выберите TOR сервер в списке VPN серверов.Редко встретишь браузер, при разработке которого продумали все до мелочей. Здесь есть и функция фонового проигрывания (можно слушать музыку с выключенным экраном), и встроенный медиаплеер, и сканер QR-кодов, и все это АНОНИМНО. Даже все данные, идущие через VPN сжимаются, чтобы сэкономить ваш мобильный трафик.Пользоваться браузером можно совершенно бесплатно, а для тех, кто хочет получить доступ к дополнительным инструментам, предусмотрена премиум-подписка. Она позволяет выбирать страну VPN, автоматически подключается к нему при запуске браузера, дает поддержку ZIP-архивов, дополнительные темы и многое другое. Обойдется не дороже чашки кофе в месяц (сейчас вообще со скидкой 50% раздают), так что есть, над чем подумать.Aloha Browser был создан для iOS и Android группой энтузиастов, которые обеспокоены текущим отношением к свободе слова и отсутствию приватности в интернете. И это видно не только по количеству функций, связанных с анонимностью в Сети, но и также пользовательской базе — миллионы уже пользуются этим приложением каждый день, как своим браузером по умолчанию. Если заботитесь о своей приватности (или просто хотите пользоваться браузером с кучей наворотов), попробуйте тоже.Название: Aloha Browser: браузер VPN TOR
Издатель/разработчик: Aloha Mobile
Цена: Бесплатно
Встроенные покупки: Да
Совместимость: Универсальное приложение
Ссылка: Установить