Кракен купить наркотики
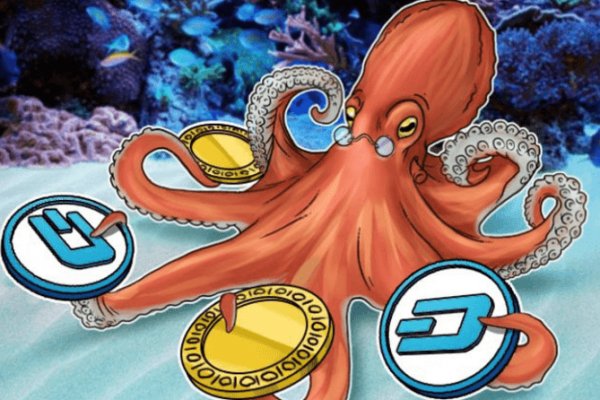
44-45, (describes cocaine/crack processing melting points.44 has «cannot be smoked becausemelting point of 190.45 has «It is the most addictive form of cocaine webpage: Google-Books-Estroff Архивная копия от на Wayback Machine. Так возникает передозировка. Торговая площадка mega Официальный сайт вход. Это важно, так как если не восстановить социальную значимость пациента он снова сорвется. Onion вход Вход в маркетплейс mega осуществляется с помощью привычного браузера ТОР. Это связано с тем, что трубки для курения кокаин-крэка очень короткие. Большое количество токсинов вызывает декомпенсацию в работе ЦНС и внутренних органов. Самым печальным последствием употребления крэка является смерть. Выведение из запоя 3 000 Вызов нарколога на дом 3 000 Признаки наркомана Человек, который употребляет крэк, имеет поврежденные сухие губы, на которых могут быть язвы, герпес или засохшие корки. Потом ставят катетер и наводняют организм потерпевшего 5 глюкозой. Если человек не употребляет органы не хотят работать как обычно. Чем дольше наркоман употребляет тем больше нужно для передозировки. Сайт кракен We will tell you about the features of the largest market in the dark web Official сайт Kraken is the largest Sunday, which is "banned" in the Russian Federation and the CIS countries, where thousands of stores operate. Это делают для удешевления наркотика и увеличения его веса. Дата обращения: 30 сентября 2017. Симптомы передозировки, следующие: нарушение сознания; изменение дыхания или вовсе его остановка; аритмия; судороги; рвота; обильное потоотделение; повышение температуры тела; сильное расширение зрачка; мышечные спазмы по всему телу; появление сильного кашля, который проходит, только чтобы пациент сделал вдох; появление галлюцинаций, иллюзий, маний, панических атак. В отличие от обычного кокаина, крэк-кокаин принимается внутрь посредством курения. Следствием этого может стать инфаркт миокарда или геморрагический инсульт. Им были предсказаны страдания от тяжёлых, необратимых нарушений, в том числе снижение интеллекта и социальных навыков. Боле правильными считаются методики лабораторного исследования крови или мочи. Физические симптомы Что происходит в организме после употребления крэка: онемение языка и глотки; повышение артериального давления; ускорение сердцебиения; нарушение движения слизи. Через общую иглу (или общую ложку, если шприц заправляется маркетплейс в ложке) могут распространяться заболевания, передающиеся половым путём, такие как, например, ВИЧ. Несчитаное количество профессионалов, будут вас сопровождать в любых вопросах. В результате дети, подвергшиеся воздействию кокаина, чаще рождаются с низкой массой тела (менее.5 кг). Морган и Циммер пишут, что имеющиеся данные свидетельствуют о том, что « курение кокаина само по себе не увеличивает заметно зависимость. Крэковые наркоманы постоянно хотят новую дозу. Все остальные манипуляции в виде аппаратной очистки, гемодиализа и инфузии проводят только в стационаре или специальных центрах реабилитации. Крэк-кокаин. Состав наркотика На вид это белые кристаллы, разного размера, легко крошатся. Официальный список наркотиков Архивная копия от на Wayback Machine правительство российской федерации постановление от. Click to enter kraken darknet Safety kraken сайт everything is done for clients of kraken darknet onion To ensure the safety of clients, Kraken сайт takes a whole range of measures to protect personal information. Эти 4-дюймовые (10 см) трубки не очень долговечны, 16 быстро ломаются, а курильщики, как правило, продолжают их использовать, хотя они становятся всё короче. Mega market Официальный сайт Площадка ОМГ работает с 2022 года и сразу нашла множество почитателей. Содержание В чистом виде крэк выглядит как белые кусочки с неровными краями и имеет плотность чуть более высокую, чем у восковой свечи. OMG сайт Официальный сайт вход Некоторые пользователи считают, что когда они что-то покупают несколько раз, они автоматически становятся постоянными клиентами. 7 Некоторые люди, принимавшие кокаин, сообщали о чувстве беспокойства, раздражительности и тревожности. Заражение при уколах : если крэк приготавливается с уксусом или лимонным соком в ложке для введения с помощью шприца, существует риск передачи ряда заболеваний. При отсутствии пульса делайте непрямой массаж сердца прямыми руками с интервалом 2 нажатия за 1 секунду. В странах Европы с США существуют целые программа для лечения таких зависимых. 12 Женщина курит крэк-кокаин. Могут добавлять левамизол (средство от гельминтов) и другие синтетические психостимуляторы. Считается, что зависимость от крэка вылечить намного сложнее, чем от любого другого психостимулятора (исключениями являются «соли для ванн. Но если они подтверждают факт употребления, то с их заключением можно идти в суд. Как остановить действие Это один из немногих наркотиков, который действует до 20 минут. Но есть еще такое явление, которое называется толерантностью.
Кракен купить наркотики - Кракен ссылка 2web
Увеличение дозы из-за примесей : поскольку качество крэка может сильно варьироваться, люди часто вынуждены курить большее количество разбавленного крэка, не подозревая, что достижение похожего состояния от новой партии крэка по сравнению с чистым может привести к передозировке, возникнут проблемы с сердцем, курильщик может потерять сознание. Кроме поражения органов, сильно страдает нервная система. Синдром отмены и как его облегчить За несколько приемов формируется стойкая психическая зависимость. Лучшие магазины уже успели разместить свои товары на сайте ОМГ. Архивировано года. Если он в сознании - давайте ему пить много жидкости (воды, сладкого чая). Описаны случаи, когда наркоманы по 3 дня курили крэк, при этом они пили только воду. После окончания действия наркотика состояние может стать абсолютно противоположным. Часто у таких больных возникают проблемы с ЖКТ и сердцем. Нельзя давать кофе и энергетики. 7 Большое количество препарата (несколько сотен миллиграммов или больше) усиливает кайф принявшего, но может также привести к странному, неустойчивому и агрессивному поведению. Дата обращения: Архивировано года. Хотя возникает устойчивость к кайфу, наркоманы могут при этом одновременно стать более чувствительными к анестетическому и судорожному эффектам кокаина без увеличения принимаемой дозы. Некоторые исследования показывают, что подвергшиеся воздействию кокаина дети имеют повышенный риск получения врождённых дефектов, в том числе дефектов мочевыводящих путей и, возможно, порок сердца. В случаях, когда начинаются проблемы с психикой и появляется депрессия обязательно принимать антидепрессанты под контролем врача. После окончания действия крэка всегда будут наблюдаться остаточные явления. Ссылка mega Мы используем сканер для входа в Tor - marketplace Если вы хотите стать частью крупнейшего воскресенья в Darknet, вам понадобится ссылка mega Tor, которая откроет доступ к магазинам. Зависимые от крэка часто лечатся в психиатрических больницах, но безрезультатно. 1 Крэк-кокаин, продаваемый на улице, может быть фальсифицирован или «отшлифован» для увеличения объёма. Levamisole Found in Patients Using Cocaine / Annals of Emergency Medicine ( рус. Вещество считается одним из самых опасных наркотиков, так как вызывает быструю зависимость и способно вызывать необратимые изменения во внутренних органах за короткий промежуток времени. Европа править править код В Великобритании крэк относится к наркотическим препаратам класса. Дают мочегонные, антиоксиданты. Если эти органы плохо функционируют, наркотик выводится дольше. Она возникает либо из-за органной недостаточности, либо из-за передозировки.
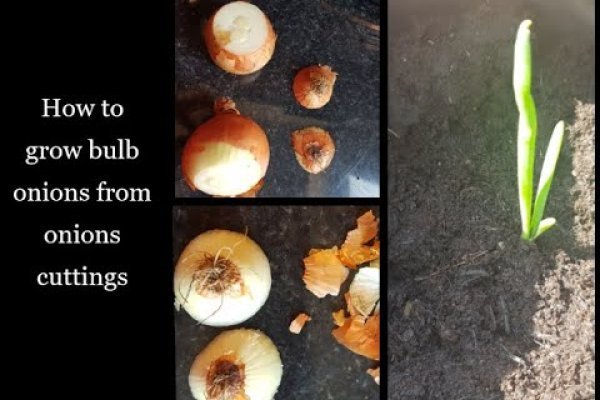
На следующей странице вводим реквизиты или адрес для вывода и подтверждаем их по электронной почте. Валюта Кракена биткоин и только им можно рассчитаться за покупку. Можно добавлять свои или чужие onion-сайты, полностью анонимное обсуждение, без регистрации, javascript не нужен. Onion сайтов без браузера Tor(Proxy) - Ссылки работают во всех браузерах. Спасибо! Pastebin / Записки Pastebin / Записки cryptorffquolzz6.onion - CrypTor одноразовые записки. Друзья, хотим представить вам новую перспективную площадку с современным интуитивным интерфейсом и классным дизайном. Напоминает slack 7qzmtqy2itl7dwuu. Нельзя не рассказать про богатый функционал маркета, всё действительно сделано на высшем уровне, всё для удобства и экономии времени пользователей. Русское сообщество. Нужно лишь зарегистрироваться на портале omg RU, атвоя информация направится на хранение в кодированном формате наоблачном компьютере. Войти без пароля в одноклассники можно, но только том случаи, если вы уже авторизировались на них ранее, для этого нужно просто перейти на одноклассники, если у вас отображается форма для входа, то значит вы не авторизированы. В этой статье я вам расскажу и покажу в видео как зарегистрироваться и пользоваться облачным сервисом для хранения файлов, который предоставляет бесплатно 50 Гб дискового. В приветственном окошке браузера нажмите. Внутри ничего нет. Используйте мобильное приложение Steam, чтобы войти с помощью QR-кода. Мы так и думали. Топ сайтов тор, или 25 лучших темных веб-сайтов на 2022 год (и как получить к ним безопасный доступ). Только английский язык. Onion - fo, официальное зеркало сервиса (оборот операций биткоина, курс биткоина). Зеркала кракен работают. Огромный вклад в развитие теневого Интернета внесла научная лаборатория US Naval Research Lab, разработавшая специальное программное обеспечение прокси-серверов, позволяющих совершать анонимные действия в интернет-сети The Onion Router, более известное как. Защита покупателя Отдавая деньги за товар вы можете быть на все сто процентов уверены в его получении.