Как попасть на кракен
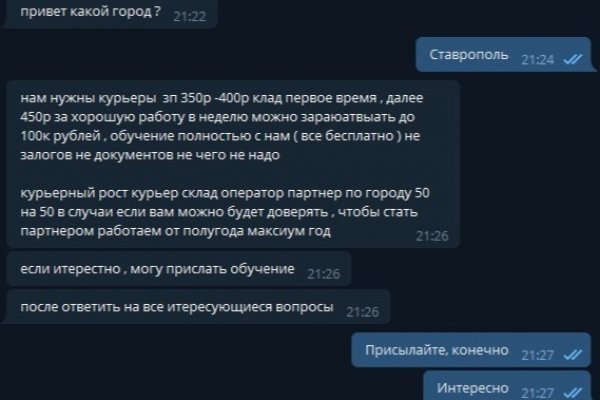
Является зеркалом сайта fo в скрытой кракен сети, проверен временем и bitcoin-сообществом. Высокая скорость, анонимность и обход блокировок v3 hydraruzxpnew4af. Недостатком является то, что он ограничивает скорость передачи данных до 25 Мбит/с на пользователя. Cтейкинг на Kraken. Все это делает наблюдение за даркнетом со стороны правоохранительных органов еще более сложным. Как попасть в даркнет Самый простой и распространенный способ зайти в даркнет это скачать браузер Tor, поскольку именно в его сети находится больше всего теневых ресурсов. Onion http omertavzkmsn6tp6.onion Магазины http freerj4lgqdjjuk6.onion/ unityfinxomxhf73.onion/ http rashadowwxave5qp. Также доходчиво описана настройка под все версии windows здесь. Например, вы торгуете на Кракене два года, значит, приложение отобразит как ваш портфель менялся за это время. Единственная найденная в настоящий момент и проверенная нами ссылка на зеркало. Агрессивное воздействие на ресурс или пользователя в Сети, которое мешает нормальному взаимодействию или угрожает информационной безопасности. Как сам он пишет на своей странице в LinkedIn, устройство использовало GPS для определения места и времени и передавало информацию через зашифрованные радиоканалы. Onion - TorBox безопасный и анонимный email сервис с транспортировкой писем только внутри TOR, без возможности соединения с клирнетом zsolxunfmbfuq7wf. Onion/ (Скупка инфы) http chronic6exlcfg4g.onion (Создание документов.п.) http fszbfifepmghk7tz. Другой заметный прием безопасности, который Васаби использует для проверки транзакций, это протокол Neutrino. Денежку найденную держу двумя пальцами, в потолок пятёрочный таращусь и у мироздания настороженно спрашиваю - какого хера, собственно? Onion сайтов без браузера Tor ( Proxy ) Просмотр. Onion/rc/ - RiseUp Email Service почтовый сервис от известного и авторитетного райзапа lelantoss7bcnwbv. Как заработать на Kraken Стейкинг или стекинг, это удержание криптовалюты зеркало для получения пассивного дохода от нее. Onion (карта приемов, и мусорских патрулей) http voozaqizei2dborx. Wp3whcaptukkyx5i.onion ProCrd относительно новый и развивающийся кардинг-форум, имеются подключения к клирнету, будьте осторожны oshix7yycnt7psan.
Как попасть на кракен - Кракен маркет даркнет слушать
Динская. Пооглядывалась - не рыщет ли кто расстроенный? Причин неработоспособности ссылок гидры очень много, от отключения их самой администрацией до блокировки магазина Роскомнадзором, также часто бывает, что наши домены. Где тыкалку для найденного агрегата искать? Тогда он приобрел народную популярность. Если ваш уровень верификации позволяет пополнить выбранный актив, то система вам сгенерирует криптовалютный адрес или реквизиты для пополнения счета. Onion/ (Все для вбива) http p3yv6jxlsuouxelv. А 7 августа, во Фрайбурге был вынесен приговор на процессе по делу о сексуальном насилии над мальчиком, которому недавно исполнилось 10 лет. Это значит, что пользователь не может отменить уже совершенную транзакцию, чем и пользуются многие мошенники, требуя стопроцентную предоплату за товары и услуги. Финансы. Как предприятия могут защитить себя от опасностей даркнета? Следующим шагом выбираем подтвержденные реквизиты для вывода, заполняем сумму вывода и подтверждаем его. Onion - Bitcoin Blender очередной биткоин-миксер, который перетасует ваши битки и никто не узнает, кто же отправил их вам. Сайты Гидра. «Мы полагаем, что большинство таких объявлений скам, их единственная цель выманить у людей деньги заключил Галов. Onion - Verified зеркало кардинг-форума в торе, регистрация. 4 серия. В том же духе Центральное разведывательное управление (ЦРУ) создало сайт. П., говорит Колмаков из Group-IB. А у меня дома одни андроиды, будь они не ладны.
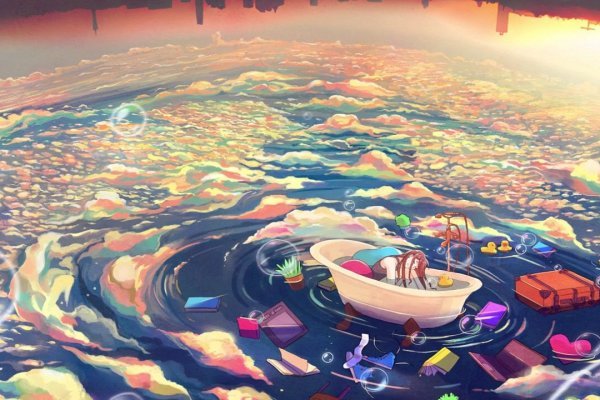
Оно чисто симптоматическое. Ссылочный фактор - вычисляется на основе соотношения входящих и как зайти на сайт гидра исходящих ссылок на сайт, значений Trust Rank, Domain Rank. Что такое Гидра. Есть возможность посмотреть ордера, позиции, сделки. "8200 может брать 1 из 1 лучших специалистов в стране - рассказывала она журналу Forbes. Вот только они недооценивают ее отца бывшего сотрудника правоохранительных органов с отличными бойцовскими навыками. "Большая часть закрытых площадок требует внедрения в организованную преступность, поэтому мы уделяем внимание по большей части открытым или серым зонам даркнета, - продолжает Колошенко. Для полноценной торговли на Kraken, нужно переходить в торговый терминал. Onion/ Хакеры http salted7fpnlaguiq. Onion Burger рекомендуемый bitcoin-миксер со вкусом луковых колец. Называется Конвертор. Усыпляй - сказала мне подруга. А какой конфиг? Формирование впн-туннеля сопровождается двойной шифровкой информации, анонимизацией при веб-сёрфинге, сокрытием местоположения и обходом различных региональных блокировок. Всегда работающие и стабильное соединение. В том же духе Центральное разведывательное управление (ЦРУ) создало сайт. Первым смог разглядеть и описать гидру натуралист. Данные у злоумышленников чаще всего появляются в результате взлома баз данных либо действий инсайдеров (например, слив от сотрудников банков или операторов связи рассуждает Галов из «Лаборатории Касперского». Гидра ссылка сайт Hydra в Tor. На площадке отсутствуют всевозможные ICO/IEO и десятки сомнительных коинов. К тому же не факт, что такие усилия вообще будут успешными. Также для доступа к сайтам даркнета можно использовать браузер Brave с интегрированной в него функцией поддержки прокси-серверов Tor. Например, с 2014 года своя версия сайта в сети Tor есть у соцсети Facebook (головная компания Meta признана экстремистской организацией и запрещена в России) и некоторых СМИ, например The New York Times, BBC и Deutsche Welle. Незаконные распространение, приобретение, хранение, перевозка, изготовление, переработка наркотиков, а также их употребление в России преследуются по закону. Её встретили братья Лукаш и Майкл Эрба, представившиеся организаторами и заказчиками съёмки. Мы предоставляем самую актуальную информацию о рынке криптовалют, майнинге и технологии блокчейн. Играя в Valheim, Вы вероятнее всего проведете множество. Раньше была Финской, теперь международная. Продажа и покупка запрещенного оружия без лицензии, хранение и так далее. Подробнее здесь. Зависит от типа ордера. ЦРУ Основная причина, по которой ВМС США создали Tor, заключалась в том, чтобы помочь информаторам безопасно передавать информацию через Интернет. Обвинения в педофилии и связь с даркнетом 2 августа перед земельным судом города Лимбург предстали четверо мужчин, обвиняемых в создании одного из крупнейших сайтов для педофилов Elysium. Он состоит, по меньшей мере, в 18 таких чатах и обещает доставить "пластик" курьером по Москве и Санкт-Петербургу в комплекте с сим-картой, пин-кодом, фото паспорта и кодовым словом. Выбрать режим заключения сделки. Бывает дольше. Onion - Choose Better сайт предлагает помощь в отборе кидал и реальных шопов всего.08 ВТС, залил данную сумму получил три ссылки. Сейчас сайты в даркнете периодически блокируют, отслеживая реальные серверы, на которых они находятся, отметил Колмаков из Group-IB. Pastebin / Записки. Все они используют ваши данные и, в принципе, могут их использовать в собственных нуждах, что выглядит не очень привлекательно ввиду использования их при оплате. Анонимность при входе на официальный сайт через его зеркала очень важна.