Kraken даркнет gigageek ru
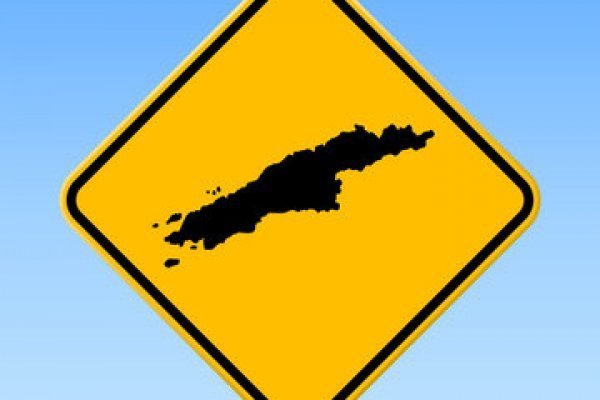
AboutUsVision & MissionCore ValuesMilestonesManagementTeamCompaniesProductsServicesCareerContactIDENThe Largest Shell LubricantsDistributor in IndonesiaThe Radiator CoolantExpertBeyond Products, GivingAssurances3000+Customers22Locations23Years of ExperienceAbout UsSEFAS began its kraken journey in 1997 as a distributor for ShellLubricants. Over the years, the company has made its mark as one ofthe leading companies in Indonesia’s lubricant supply chain.More InfoCompaniesProductsOilGreaseCoolantDegreaserServicesWe provide a wide portfolio of services как revolving aroundapplication and management of lubricant products, equipped withdedicated and reliable technical experts who are ready to servecustomers.More [email protected] UsCompaniesProductsServicesCareerContactCopyright © 2022 Sefas Group
Kraken даркнет gigageek ru - Магазины с наркотиками
( зеркала и аналоги The Hidden Wiki) Сайты со списками ссылок Tor ( зеркала и аналоги The Hidden Wiki) torlinkbgs6aabns. Сообщения, анонимные ящики (коммуникации). Является зеркалом сайта fo в скрытой сети, проверен временем и bitcoin-сообществом. Onion - Verified,.onion зеркало кардинг форума, стоимость регистрации. Onion - Bitcoin Blender очередной биткоин-миксер, который перетасует ваши битки и никто не узнает, кто же отправил их вам. Вместо 16 символов будет. . Underdj5ziov3ic7.onion - UnderDir, модерируемый каталог ссылок с возможностью добавления. Мы выступаем за свободу слова. Mixermikevpntu2o.onion - MixerMoney bitcoin миксер.0, получите чистые монеты с бирж Китая, ЕС, США. Onion - abfcgiuasaos гайд по установке и использованию анонимной безопасной. Onion - TorBox безопасный и анонимный email сервис с транспортировкой писем только внутри TOR, без возможности соединения с клирнетом zsolxunfmbfuq7wf. Площадка позволяет монетизировать основной ценностный актив XXI века значимую достоверную информацию. Обратите внимание, года будет выпущен новый клиент Tor. Onion - OnionDir, модерируемый каталог ссылок с возможностью добавления. Onion/ - форум FreeHacks Ссылка удалена по притензии роскомнадзора Ссылка удалена по притензии роскомнадзора Сообщения, Анонимные Ящики (коммуникации) Сообщения, анонимные ящики (коммуникации) bah37war75xzkpla. Onion - WWH club кардинг форум на русском языке verified2ebdpvms. На момент публикации все ссылки работали(171 рабочая ссылка). Vabu56j2ep2rwv3b.onion - Russian cypherpunks community Русское общество шифропанков в сети TOR. Onion - onelon, анонимные блоги без цензуры. Перемешает ваши биточки, что мать родная не узнает. I2p, оче медленно грузится. Есть закрытые площадки типа russian anonymous marketplace, но на данный момент ramp russian anonymous marketplace уже более 3 месяцев не доступна из за ддос атак. Hiremew3tryzea3d.onion/ - HireMe Первый сайт для поиска работы в дипвебе. Есть много полезного материала для новичков. Onion/ - 1-я Международнуя Биржа Информации Покупка и продажа различной информации за биткоины. Foggeddriztrcar2.onion - Bitcoin Fog микс-сервис для очистки биткоинов, наиболее старый и проверенный, хотя кое-где попадаются отзывы, что это скам и очищенные биткоины так и не при приходят их владельцам. Pastebin / Записки. По слухам основной партнер и поставщик, а так же основная часть магазинов переехала на торговую биржу. Частично хакнута, поосторожней. p/tor/192-sajty-seti-tor-poisk-v-darknet-sajty-tor2 *источники ссылок http doe6ypf2fcyznaq5.onion, / *просим сообщать о нерабочих ссылках внизу в комментариях! Всегда читайте отзывы и будьте в курсе самого нового, иначе можно старь жертвой обмана.
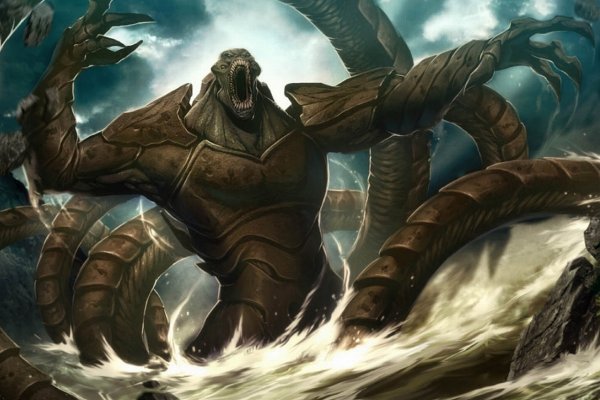
Нас интересует пункт "Connect to Tor" Подключение к сети Tor выбираем его. Spotflux - это простой в использовании клиент для Mac и ПК (скоро появится и мобильная связь). Переполнена багами! Кракен курган сайт kraken ssylka onion, как правильно войти в kraken, kraken union официальный сайт ссылка, правильное зеркало крамп kraken ssylka onion, вход на kraken в обход блокировки, новое зеркало крамп kraken ssylka onion, кракен войти через тор. Есть немало приложений с неплохой оценкой: Tor web Browser, vpntor, Луковка. Это один из первых русскоязычных форумов для киберпреступников. Начинание анончика, пожелаем ему всяческой удачи. Для этого скопируйте адрес вашего кошелька на площадке и впишите его на сайте, откуда будет делаться перевод. Как определить неисправность регулятора давления? В октябре 2021. Цена на эти услуги зависит от сложности задачи. В этой статье мы расскажем вам, как скачать. Новая площадка для дилеров и покупателей. Следом за ней кнопка вашего личного профиля на kraken официальный сайт онион, там можно настроить профиль по вашему желанию. Onion Daniel Winzen хороший e-mail сервис в зоне. Настоящая ссылка зеркала только одна. Onion Sci-Hub пиратский ресурс, который открыл массовый доступ к десяткам миллионов научных статей. Аналоги Альтернатив Тор браузеру для iOS существует множество и все они доступны для скачивания в AppStore. ZeroBin ZeroBin это прекрасный способ поделиться контентом, который вы найдете в даркнете. Является зеркалом сайта fo в скрытой сети, проверен временем и bitcoin-сообществом. Более дорогие сервисы могут сжимать трафик, кэшировать файлы и даже блокировать назойливую рекламу. Самое главное что могу вам посоветовать. Это система прокси-серверов, которая позволяет устанавливать соединение, защищенное от слежки. А также увеличит дневные лимиты на вывод в криптовалюте до 500000 и в фиате до 100000. Мы создали условия для максимально комфортной игры и ждем вас и ваших друзей на нашем новом острове! Кракен онион сайт тор Ссылки крамп. После того, как информация о даркнете и TORе распространилась, резко возросло и число пользователей теневого Интернета. Onion/?x1 - runion форум, есть что почитать vvvvvvvv766nz273.onion - НС форум. Уровни верификации на Кракен: Базовый уровень доступен ввод и вывод криптовалюты (ограничение на вывод до 5000 в день, эквивалент в криптовалюте). Если не учитывать краткосрочные падения сайта, площадка работает стабильно и имеет высокую надежность. В окне котировок нажать на BUY напротив необходимой к покупке криптовалюте. Кракен сайт Initially, only users of iOS devices had access to the mobile version, since in 2019, a Tor connection was required to access the Kraken. Выбирайте любое kraken зеркало, не останавливайтесь только на одном. 243 ZenMate ZenMate - это простой в использовании плагин для браузера, который обеспечивает VPN - шифрование для вашего браузера. 77 ProtonVPN VPN, ориентированный на безопасность, разработанный учеными cern из команды ProtonMail. Не получается зайти на Кракен, что делать? Эти сайты находятся в специальной псевдодоменной зоне. У сайта кракен тысячи (если не миллионы) постоянных покупателей к которым относятся очень лояльно. Гидра онион сайт. Нужно знать работает ли сайт.